The cabinets look refined, handcrafted by old world techniques. And, while the company says it employs some of the best cabinetmakers in the area, that doesn’t mean that Village Handcrafted Cabinetry doesn’t utilize new technology to achieve that custom cabinet look.
Family-owned and operated for more than three decades, the Lansdale, Pennsylvania, company creates custom products from start to finish. They design, build, finish and install all their cabinets. Custom products include bathroom vanities, cabinet doors, cabinets, custom kitchens, pantries, walk-in closets, kitchen design, kitchen remodeling, laundry room design, and pantry design.
The company, which is just north of Philadelphia, started as a one-man shop and now has grown to more than 60,000 square feet of manufacturing space. Company owner, and founder, Joseph Trave, said Village Handcrafted Cabinetry focuses on mid- to high-end residential cabinetry, working primarily with the trade, designers, builders, remodelers, and a small percent of retail customers. Most of the company’s clients are in eastern Pennsylvania,
Beginnings
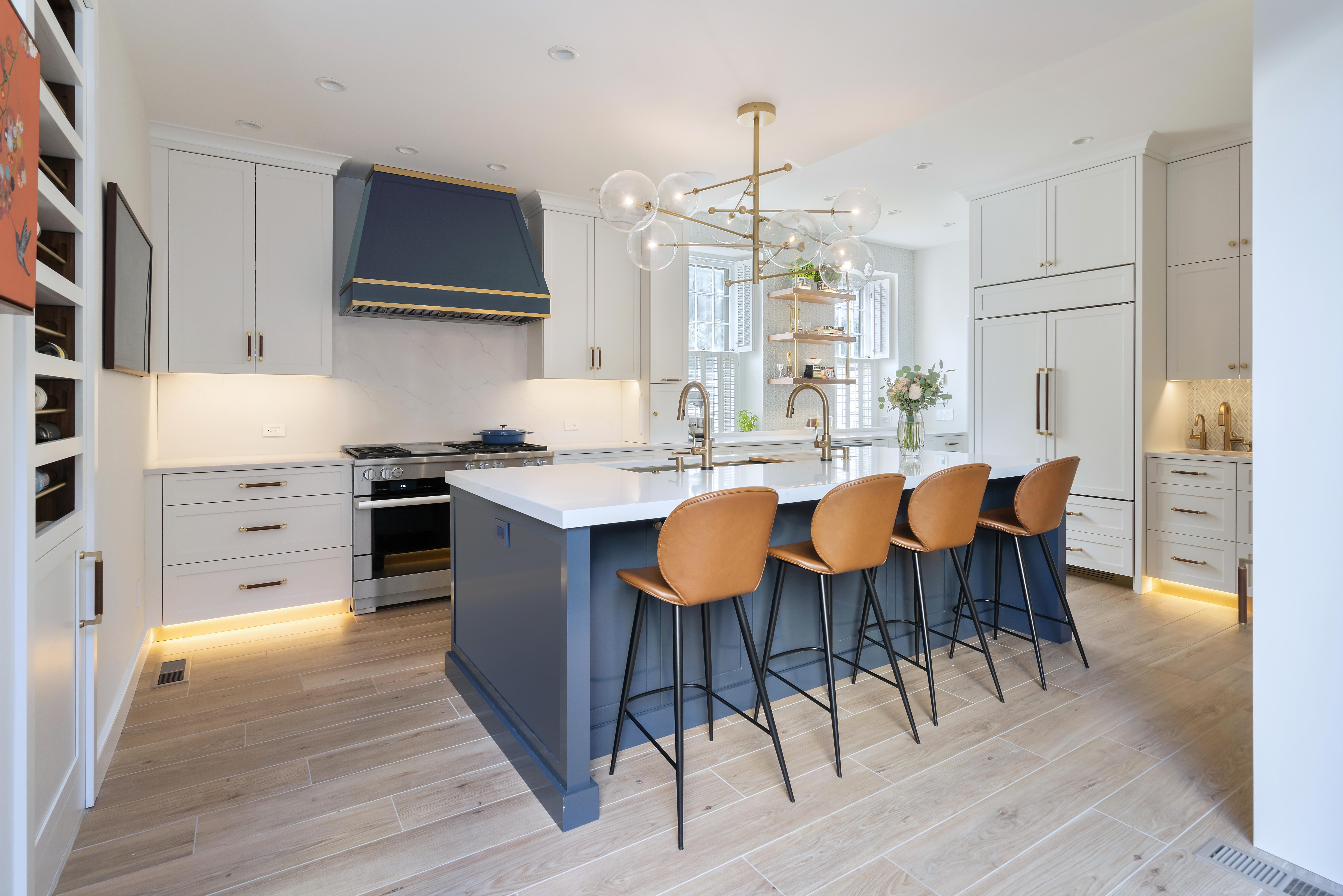
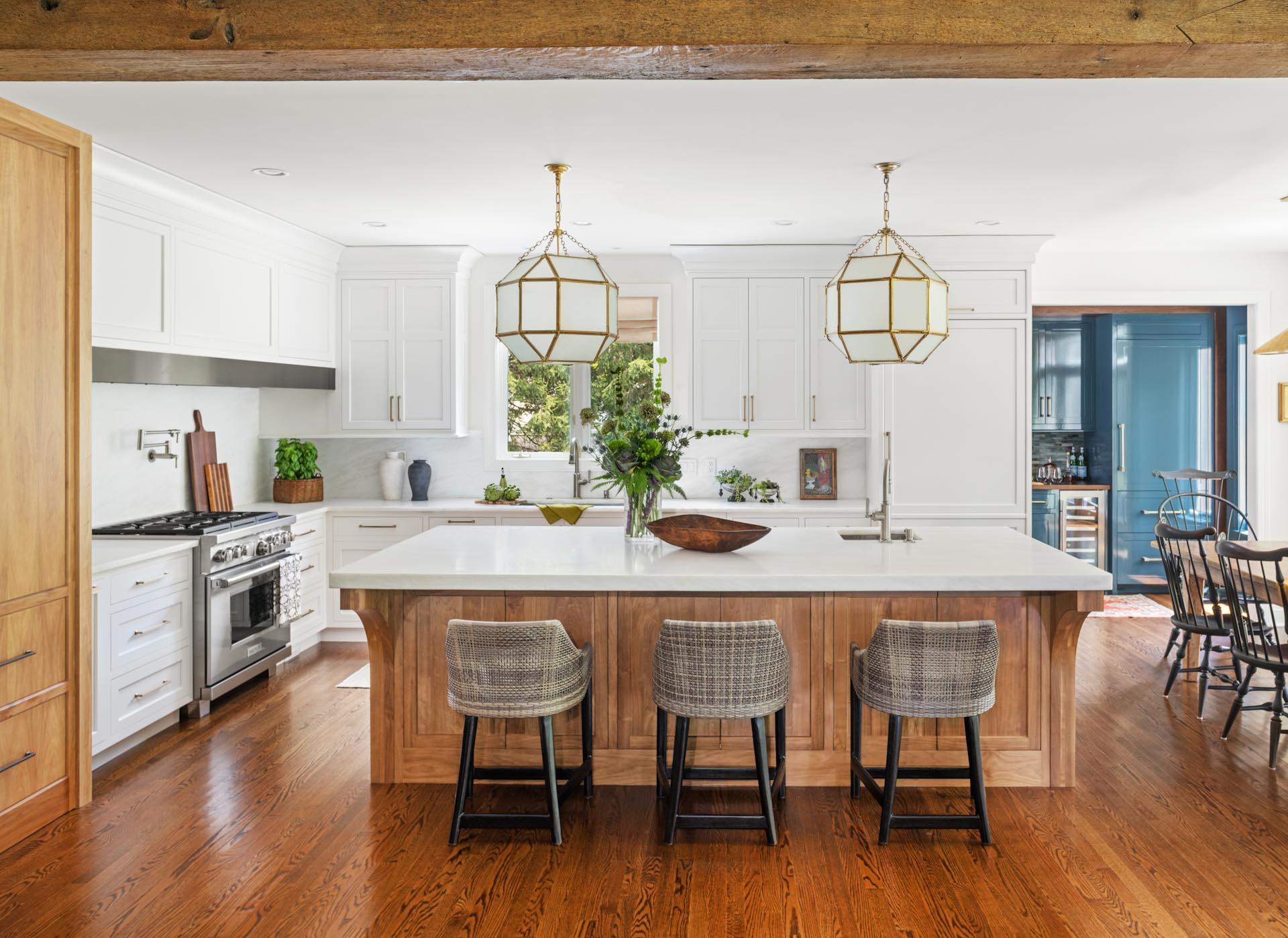
Trave said that he has always been “extremely passionate about cabinetry and woodworking,” having started building furniture in the family’s backyard when he was 16 years old. “I had a pencil behind my ear when I was seven, literally, and wore a nail pouch. I always wanted to be a carpenter.”
Trave worked in his family restaurant business for a couple of years before realizing that he wanted to open his own shop. “I decided that’s what I wanted to do for the rest of my life,” he said. “I like building things, and now the cool thing is I’m building a business around it.”
Founded in 2000 as Village Handcrafted Cabinetry, Travis spent three years working out of his parents’ 400-sq.-ft. garage. In 2003 he met a local cabinetmaker looking to sell his business, Village Woodshop, in Quakertown, Pennsylvania. Trave bought the shop’s machinery, took over the rent and kept two employees.
After renaming the Village Woodshop company to Village Handcrafted Cabinetry, the company moved to Lansdale in 2006, opening a showroom and production facility.
Over the years, the custom kitchen cabinet and architectural millwork firm has grown and expanded, starting from the 400-square-foot garage and now topping out to 70,000 square feet, including about 60,000 square feet of manufacturing space.
His wife, Gina, joined the firm, and the company took on partners, Gary and Jennifer Marks. Through the years, the company has faced recession and economic downturns and a pandemic, but the four-person management team dug in and saved the business; even at one point having to mortgage their homes.
The management team consists of Trave, who is the owner, CEO and director of sales. His wife, Gina, is the director of marketing, Gary Marks is director of finance and purchasing, and Jennifer Marks is director of Human resources/payroll.
Production
Most products are done completely in house. All construction is mortise and tenon. Village also does its own mouldings, has 1,200 profiles, and can create any kind of profile. In one section of the production floor is a library of hundreds of cutter profiles. Matching an existing appearance is a common assignment for them.
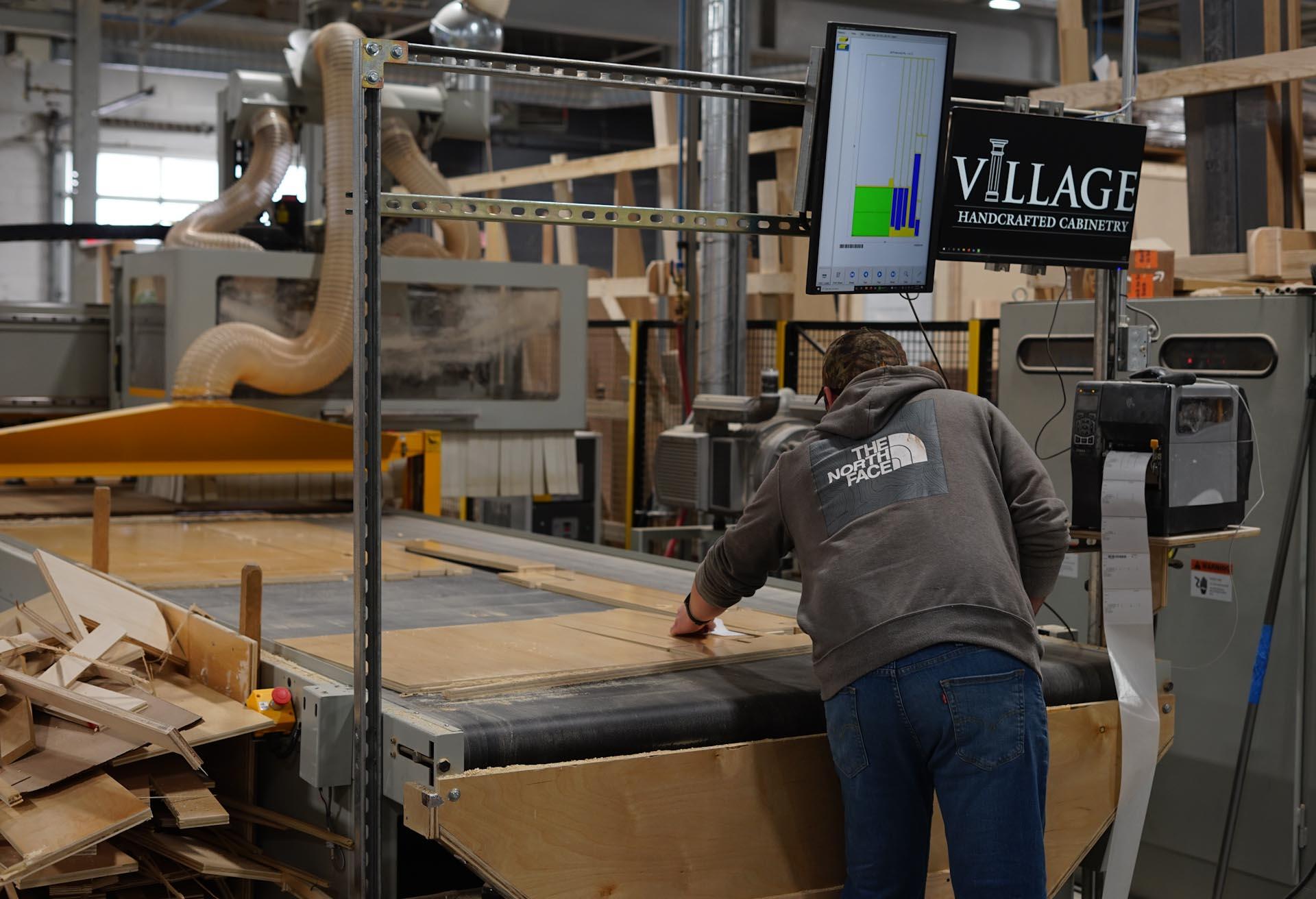

Whatever the customer wants, essentially. At Village Handcrafted Cabinetry, Trave said, the company has one goal: To help our clients build spaces that fuse comfort with class and convenience.
Some of their growth is in the equipment that the company has invested in. They use CNC equipment for panel processing and sold wood machining.
The panel processing area was abuzz with sound as panels are uploaded and machined using CNC equipment. Nested panels were being processed. Raised panel doors produced.
Production equipment includes a Stratos 3-axis machining center and a Weeke Vantage 2000 CNC processing center. Automated loaders onload and offload panels and parts.
“Panels are loaded from the front with an automatic loader so the operator doesn’t have to leave the tail end of the machine,” said Trave.
The company added TigerStop stations to produce all of its stiles and rails and put in a miter fold machine. “All of our corners and face frames are miter folded together, which is a really nice feature,” he said.
Sanding equipment includes a Timesavers multi-head flat sander as well as a MB Roba Tech sander used for the sanding of flat and profile surfaced parts.
A state-of-the-art dust collection system is connected to all the production machines, gathering sawdust in a silo. The collected waste eventually is burned to heat the facility during winter.
The company has an in-house finishing lab, and can do color matching. Clients often bring in challenging finishing jobs, said Trave. In the lab, or finishing kitchen as Travel calls it, bright lights illuminate the area where workers make samples for custom colors.
“It’s all ‘by the eye’ here,” he said. “A lot of these people are true artists. They’re looking at every sample. The customer will sign off on the sample and they keep half of a color block and we have half so we’re making sure every color looks the same.”
One of the newer production areas is a small in-house metalworking shop. “We’re doing very minor fabrication for our hoods and for our floating shelves, anything that requires minor metal work,” said Trave. “It’s separated from the woodworking, obviously for sparks, you know and for fire safety.”
Future expansion?
The company has about 60,000 square feet of production space and “we are full,” Trave said. “We are building approximately seven to 10 kitchens a week, so it fills up very fast.”
Trave said that while he doesn’t build cabinets anymore, “I get to go out and see amazing cabinets that we build.”
Watching the company grow is exciting and Trave said the company has plans for further growth.
“I am super excited about the next seven to 10 years and, and even beyond that,” he said. “I don’t know where it’ll go, you know, whether it will continue to grow by maybe purchasing another company or having a secondary facility somewhere.” ✚
Have something to say? Share your thoughts with us in the comments below.